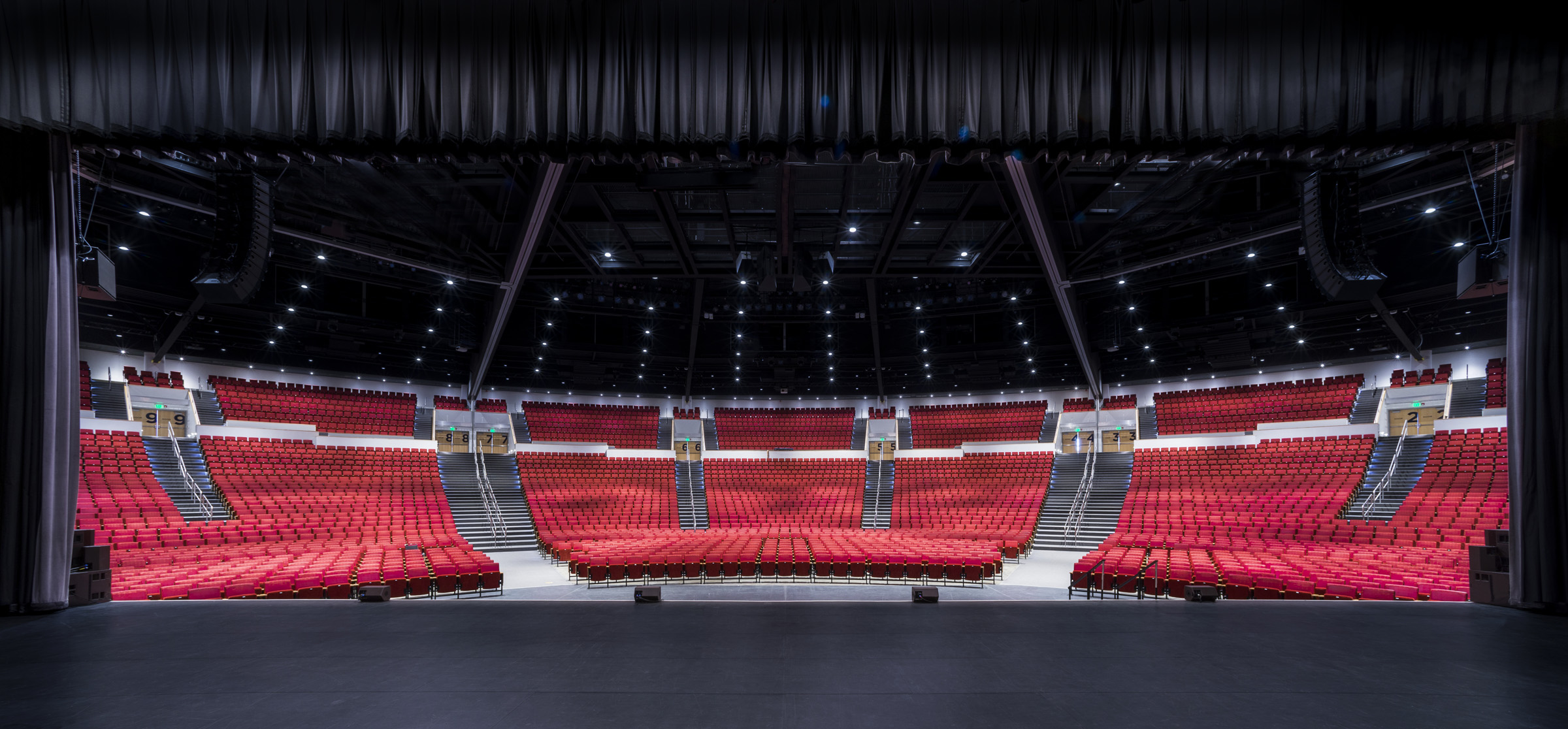
Bellco Theatre
Location: Colorado Convention Center; Denver, Colorado
Venue Type: 5,000-Seat Proscenium Theater
Application: House Lighting Retrofit for Energy and Performance
Venue Representative: Dave Clow, Technical Services Supervisor
Vendor/System Engineering: Oasis Stage Werks – Gary “Frog” Justesen
Lighting Representative Agency: CT Lighting Sales – Jason Humphrey
The Bellco Theatre (formerly the Wells Fargo Theatre) is a 5,000-seat venue located within the Colorado Convention Center complex and operated by SMG in Denver, Colorado. As one of the largest proscenium theater venues in the state of Colorado, it hosts a tightly-packed schedule of civic, corporate, political and private events, and touring shows ranging from family shows to rock & roll concerts.
The Bellco Theatre was designed as a “road house,” with a solid foundation of technical equipment and a large stage to support the enormous sets and staging of the large events. The house lighting consisted of more than one hundred 500w Quartz Halogen reflector downlights, controlled by a conventional dimming system. The fixture height ranges from 10 feet to 40 feet above the audience seating. Although it provided basic functional house lighting, the original system had some issues. Illumination levels were relatively low, and uneven light distribution resulted in significantly brighter and darker areas. There were particular issues with the rear of the house, in the upper seats; here the fixtures created small, bright pools of light leaving much of the upper seating in relative darkness. With a relatively short lamp life, the fixtures required constant maintenance to change burnt-out lamps. Accessing the fixtures for re-lamping was time consuming and labor intensive, sometimes requiring the installation of scaffolding and the use of man-lifts. And finally, the last issue is a familiar one: the need to reduce energy consumption.
After 25 years at the convention center, SMG’s Technical Services Supervisor Dave Clow knew that there were options available in LED lighting that could solve these challenges and save on energy usage. Dave contacted Oasis Stage Werks to solicit a solution to improve the performance and maintenance issues that the venue had experienced since opening. After reviewing a number of options with the facility staff, Oasis recommended the Altman Chalice LED down light as the best possible solution. They had used the Chalice for similar challenges in smaller venues to great success; the same solution translated to a larger venue. Working closely with CT Lighting Sales, Altman Lighting’s representative in Colorado, Oasis presented a design to upgrade the house lighting to LED fixtures, including complete photometric studies illustrating the predicted illuminance levels.
The new design used a one-to-one replacement of the existing 500w Quartz Halogen fixtures located 40 feet above the main orchestra seating areas, with 100w Altman Chalice LED fixtures. For the rear seating areas, with a lower ‘ceiling’, the 50-Watt Chalice fixtures were chosen for installation. The Chalice offers a choice of glass or holographic lensing options that can be changed easily in the field for fine-tuning lighting coverage after the system has been installed. This application required a mix of glass wide flood and medium flood lenses in the high ceiling areas, and holographic 60° lenses to provide the optimal spread of light in the rear seating areas. SMG’s Dave Clow comments: “Our lighting levels in the main orchestra seating increased from a range of 12 – 25 foot candles to a new range of 25 – 40 footcandles. The difference in evenness in the upper seating areas is amazing. The room is visually more alive and interesting. We also eliminated the need for labor-intensive lamp replacement, and reduced electrical power for house lighting by nearly 80%. The hidden savings is the big drop in heat produced by the fixtures, which significantly reduces our air conditioning load. We are more than pleased with the results!”
How would Altman LED fixtures perform compared to the old fixtures?
At the beginning of the project the integration of LED house lights was a concern. How would LED fixtures perform compared to the old fixtures? How hard would they be to install? Would they require a special control system, or new wiring? The original system used a bank of 20-Amp theatrical dimmers to control more than 50 kilowatts of conventional fixtures. The versatile Chalice fixture comes with two options for control: digital control via DMX-512 protocol, or directMains Dimming. For new installations, the DMX version is preferable because it provides full-range dimming without the need for dimmers. But for retrofit installations with pre-existing dimmers, adding new DMX control wiring can increase the installation effort and cost. The Mains Dimming Chalice down lights are compatible with the forward-phase dimmers that are typically found in performance venues. They can be installed on the existing power wiring and run off the existing dimmers, just like the old fixtures; no new wiring is needed for the installation.
The choice of Mains Dimming for the Bellco Theater also provided superior dimming performance—smooth, flicker-free dimming via the existing dimmers. Most theaters require digital control via DMX to provide smooth dimming at the bottom of the dimming curve—that last fade from 10% to off. Mains Dimming has a low cut-off of approximately 5%, but Oasis was able to implement a custom configuration of the dimming rack to reduce the cut-off to close to 1%. Gary “Frog” Justesen of Oasis Stage Werks explains, “Different venues have different requirements for the low end of the dimming curve, based on the kind of shows they do. Traditional theaters at universities and colleges need that bottom end of the dimming curve. The Bellco did not require “fade to zero” dimming; the priority was to use the existing wiring for a simplified, fast installation. Yet we nearly achieved 1% dimming through programming a custom dimming curve that we configured in the rack for the house light dimmers.”
To further streamline the installation, Oasis and Altman worked together to confirm existing mounting conditions, and developed custom solutions that would save time for the installing contractor. One example was a special mounting adaptation that allowed the contractor to re-use the existing fixtures’ stems. The original plan was to replace the stems entirely, which would have required the contractor to work at the upper height of the ceiling trusses, another 10-12 feet higher and requiring specialized access equipment. Altman’s ability to quickly create custom metal solutions at the factory in Yonkers, NY provided for a custom solution that simplified the installation, saving time (and money) on the renovation.
The installation schedule presented the ultimate challenge for the project. The theater’s calendar runs a constant series of back-to-back events. The only time allotted for any renovation work would be in the three-week period over the Christmas and New Year’s holidays. And due to an even tighter pre-holiday schedule, the delivery of the new fixtures would have to occur on a specific date—December 9, weeks before the installation was to begin. Upon finalizing the design in early November, and despite the Thanksgiving holiday, Altman was able to ship the customized fixtures four calendar weeks after release of the order, delivering precisely on the date requested. When the installation commenced weeks later, the 140+ fixtures were installed without a single malfunctioning unit — all fixtures worked perfectly out of the box.
The combination of no new wiring, custom hardware to simplify installation, and zero defects meant that the installation happened as planned, actually completing ahead of schedule. “I never imagined it would be such a trouble-free installation,” adds Dave Clow. “The thorough planning and quality of the team enabled a flawlessly executed project. The vendor coordinated the technical details and logistics, the manufacturer delivered a custom solution with no product issues—on time as promised—, and the EC installed the equipment as planned. And the results show. The new system performs better, requires virtually no maintenance, and reduces our operating costs to a fraction of the previous system.”
For more information about the Altman Chalice down light, and Altman’s entire line of theatrical and architectural fixtures and accessories, go to www.altmanlighting.com. For more information about SMG, visit www.smgworld.com